Контроль сварных соединений
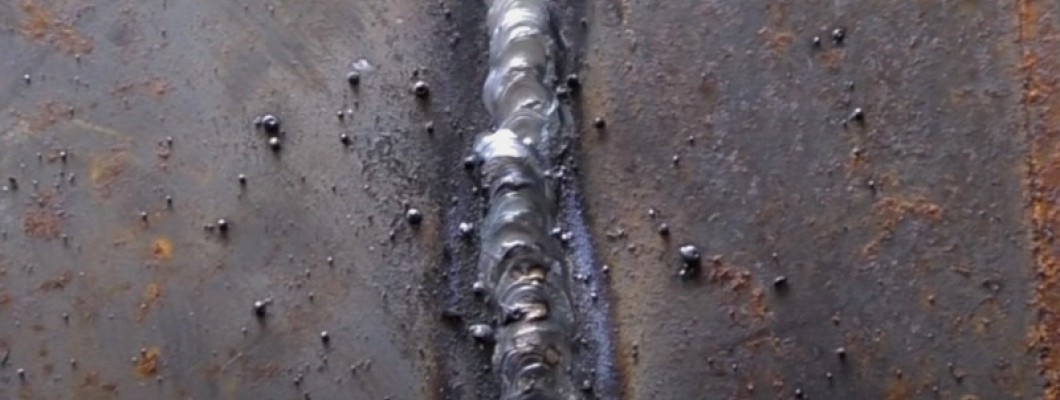
По окончании сварки важно провести контроль состояния полученных соединений. Это важно с точки зрения требований и проверки на соответствие нормативам, на наличие дефектов – очевидных и скрытых. Сварка всегда должна сопровождаться контрольными мероприятиями.
Разновидности неразрушающего контроля сварки
Выбор методики зависит от возможностей и специфики предприятия, ответственности конструкции. Сегодня используются разные виды контроля, распространенных на практике:
1. Визуальный. Простейший и первичный метод, с него начинают все контрольные операции. Этот подход помогает быстро отбраковать явно неудачные детали, экономит время и силы. Неразрушающий, используется для оценки геометрии шва. Используется лупа, штангенциркуль, шаблоны производства для проверки на соответствие стандартам.
2. Капиллярный (ПВК). Используются проникающие вещества в соответствии с ГОСТ 18442 для черных и цветных металлов. Не разрушает поверхность детали, раствор индикатора или пенетранта проникает внутрь через микроскопические поры. Обнаруживаются мелкие трещины и дефекты, а состав стоит недорого и вполне универсален, оборудование тут не требуется. Можно применять в режиме дефектоскопии, в комбинированном или простом варианте. При дефектоскопии поверхность чистят, сушат, наносят пенетрант и делают промежуточную очистку, затем наносят проявитель. Делается осмотр и анализ результатов.
3. Контроль герметичности позволяет оценить степень непроницаемости и отсутствие пропуска жидких и газообразных веществ. Он включает несколько разновидностей проверок: испытание керосином или аммиаком, проверка течеискателем, пневматический или гидравлический контроль. Обеспечивается создание избыточного давления или разрежения воздушной среды для выявления протечек. Используются манометры, специальные клапаны и оборудование для нагнетания давления, свойство керосина подниматься вверх по трещинам).
4. Магнитная дефектоскопия. Актуальный метод для изделий с ферромагнитными свойствами и составом. Обнаруживает инородные включения и мелкие трещины. Зона рассеяния с образованием полюсов на краях приводит к искажению магнетизма и плотности магнитного поля. В работе используется специальный дефектоскоп и намагничивание – циркулярное или продольное, комбинированное. Применяются магнитные порошки (в сухом или маслянистом виде, в суспензии), магнитография на основе ленты с магнитным носителем, индукционный контроль с помощью индукционных катушек, гальванометра или специальной лампы.
5. Ультразвуковой контроль – подходит для швов из разных металлов, позволяет найти дефектные структуры за счет отражения ультразвуковых волн от трещин и сколов благодаря акустическим особенностям. Используется специальный диагностический сканер и разные способы: теневой или зеркально-теневой, эхо-импульсный или эхо-зеркальный, дельта-метод. Выявляются непровары и неплавленные места, неровности и трещины, расслоения, поры внутри шва, свищи и коррозия. Можно обнаружить несоответствия геометрических размеров и повреждения, провисания, окислы.
6. Радиационный контроль. Просвечивание шва рентгеном и гамма-лучами – возможность найти самые тонкие и мелкие трещины и непроваренные места внутри и в околошовной зоне. Ионизирующее излучение позволяет анализировать итоги взаимодействия с изучаемой поверхностью. Радиография требует наличия специального аппарата для создания снимков, а также дефектометра – пластинки с канавками разной глубины. Гаммаграфический контроль и радиография являются самыми малодоступными и сложными методами контроля шва, но отличаются отличной чувствительностью, наглядностью результата, замерами глубины дефектных областей. Также используются компьютеры для цифровой радиографии.
7. Разрушающий контроль. К этому типу проверок можно отнести разные варианты испытаний: механические и химические, физические, а также металлографические. Деталь сверлят, травят растворами из аммония и хлорида меди. Химический анализ дает информацию о соответствии состава сплава и сварного шва требованиям и нормативам.
Добавлен комментарий